Курсовая работа: Точные расчеты
Курсовая работа: Точные расчеты
Курсовая
работа
по
дисциплине:
"Метрология,
стандартизация и сертификация"
на тему: "Точные
расчеты"
Содержание
1.
Расчет калибров для контроля размеров цилиндрических поверхностей
2.
Расчет посадки с зазором
3.
расчет посадки с натягом
4.
Расчет размерных цепей
Литература
1.
Расчет калибров для контроля размеров цилиндрических поверхностей
Задание: Определить
предельные и исполнительные размеры калибров для контроля отверстия Æ 17F9, вала Æ 17h9 и
контркалибров к ним. Построить схему расположения полей допусков деталей и
калибров для их контроля.
Расчет размеров
калибра-пробки для контроля отверстия Æ 17F9.
Выписываем предельные отклонения
из табл. 1.36 /1/ отверстия Æ 17F9:
ES = +59 мкм, EI = +16 мкм.
Предельные размеры
отверстия /4/:
Dmax = D + ES =
17,000 + 0,059 = 17,059 мм,
где: Dmax – наибольший предельный размер
отверстия, мм,
D – номинальный размер соединения, мм,
ES – верхнее предельное отклонение
размера отверстия, мм.
Dmin = D+EI = 17,000 +
0,016 = 17,016 мм
Размеры проходного
(ПР) и непроходного (НЕ) калибров, служащие для отсчета отклонений /4/:
ПР=Dmin=17,016
мм;
НЕ=Dmax=17,059
мм.
Данные для расчета
калибра-пробки (табл. 8.1 /4/):
Z=8 мкм, Y=0 мкм, H=3 мкм,  =0
Предельные
размеры проходной стороны нового калибра /7/:
ПРmax= ;
ПРmin= .
Исполнительный
размер проходной стороны калибра, проставляемый на рабочем чертеже:
ПРисп.= .
Изношенный размер
калибра /4/:
ПРизнош.= .
Рассчитаем предельные
размеры непроходной стороны нового калибра по формулам 1.5 и 1.6 /4/:
НЕmin= ;
НЕmax= .
Исполнительный размер
непроходной стороны:
НЕисп.= .
Произведем расчет
размеров калибра-скобы для контроля вала Æ 17h9.
Предельные отклонения
вала Æ 17h9 (табл. 1.35 /1/:
ei=-0,043 мм, es=0 мм.
Определяем предельные
размеры вала:
dmax = ;
dmin = .
Определим размеры
проходной (ПР) и непроходной (НЕ) стороны калибра-скобы, служащие для отсчета
отклонений:
ПР=dmax=17,000мм;
НЕ=dmin=16,957мм.
Данные для расчета
калибра-скобы выписываем из таблицы 8.1 /4/:
Z1=8 мкм, Y1=0 мкм, a1=0 мкм, H1=5 мкм, Hp=2 мкм.
Рассчитаем предельные
размеры проходной стороны калибра-скобы:
ПРmax = ;
ПРmin = .
Исполнительный размер
проходной стороны калибра по формуле (1.10) /4/:
ПРисп.= .
Изношенный размер
проходной стороны калибра по формуле (1.11) /4/:
ПРизнош.= .
Предельные размеры
непроходной стороны калибра-скобы по формулам (1.12) и (1.13) /4/:
НЕmin= ;
НЕmax= .
Исполнительный размер
непроходной стороны калибра по формуле:
НЕисп.=
Расчет размеров
контрольного калибра для скобы (контркалибра).
Рассчитаем предельные
размеры проходной стороны калибра по формулам (1.15) и (1.16) /4/:
К-ПРmin= ;
К-ПРmax= .
Исполнительный размер
проходной стороны контркалибра по формуле:
К-ПРисп.= .
Предельные размеры
контркалибра для контроля износа по формулам:
К-Иmax= ;
K-Иmin= .
К-Иисп.= .
Предельные размеры
непроходной стороны контркалибра:
К-НЕmax= ;
К-НЕmin= .
Исполнительный размер
непроходной стороны контркалибра:
К-НЕисп.=
Схемы расположения полей
допусков отверстия и калибра-пробки, вала и калибра-скобы и контркалибра
приведены на рис.1.1, 1.2 и 1.3.
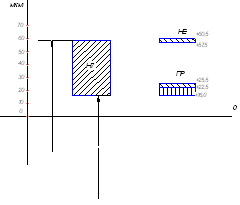
Рис. 1.1. Схема
расположения полей допусков отверстия Æ17F9 и полей
допусков калибра-пробки для его контроля
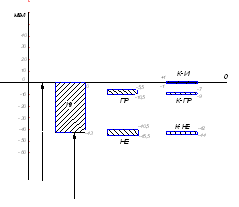
Рис. 1.2. Схема
расположения полей допусков вала Æ17h9, калибра-скобы
и контркалибра к нему
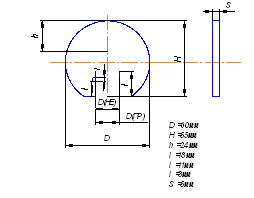
Рис.1.3. Эскиз
калибр-скобы
2. Расчет посадки с
зазором
Задание.
Подобрать посадку для подшипника скольжения, работающего длительное время с
постоянным числом оборотов n = 1000 об/мин и радиальной нагрузкой R = 3000 Н. Диаметр
шипа (вала) d = 80 мм, длина l = 95 мм, смазка – масло
сепаратное Т. Подшипник разъемный половинный (с углом охвата 1800),
материал вкладыша подшипника – БрАЖ9-4 с шероховатостью Rz1 = 3,2 мкм,
материал цапфы (вала) – сталь 40 с шероховатостью Rz2 = 1,25 мкм.
Находим
среднее давление по формуле 2.9 /4/:

Находим
угловую скорость вращения вала по формуле 2.6 /4/:

Для сепараторного
масла по таблице 8.2 находим 500=0,014 Па×с и значение степени n=1,85 из таблицы 8.3. Принимаем для
наименьшего функционального зазора SminF t=700С и
определяем 1= 700
по формуле:

Из
таблицы 8.4 /4/ для и угла охвата =1800
находим k=0,972 и m=0,972. Определяем критическую толщину масляного
слоя по формуле (2.4) /4/, принимая kж.т.=2

Определяем
предельный минимальный функциональный зазор по формуле 2.7 /4/, подставляя в
нее значения соответствующих параметров:

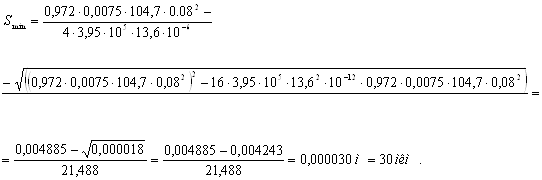
По
таблице выбираем посадку по SminF = 30мкм.
Скользящих посадок выбирать не следует, т.к. они не имеют гарантированного
зазора (Smin= 0) и применяются главным образом для
центрирования. Ближайшей посадкой будет посадка Æ80Н7/f7 c наименьшим
зазором Smin = 36мкм (табл.
1.47 /1/, предпочтительные поля допусков).
При
малых зазорах могут возникнуть самовозбуждающиеся колебания в подшипнике; если , создается возможность
вибрации вала и, значит, неустойчивого режима работы подшипника. Таких значений
следует
избегать.
Определим
значение для
выбранной посадки.
Сначала
находим относительный зазор :
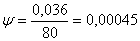
Из
уравнения (2.9) /4/ находим коэффициент нагруженности подшипника

И уже
из уравнения (2.10) /4/ определяем 

Как
уже говорилось, таких посадок следует избегать.
Выбираем
другую ближайшую посадку из табл.1.47 /1/: Æ80H7/e8. Для этой
посадки Smin=72мкм.
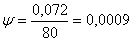


Условие
выполняется.
Здесь
нужно учесть, что мы производим расчет для наихудшего (маловероятного) случая,
когда в соединении "цапфа-вкладыш" при сборке получен минимальный
зазор Smin.
Поэтому
проверим, обеспечивается ли для выбранной посадки (Æ80H7/e8, SminТ=72мкм, SmaxТ=161мкм)
при Smin жидкостное
трение.
Для
этого определим наименьшую толщину масляного слоя по уравнению (2.2) /4/:

а
затем найдем запас надежности по толщине масляного слоя из формулы (2.4) /4/:

Расчет
показывает, что посадка по наименьшему зазору выбрана правильно, так как при Smin=72мкм
обеспечивается жидкостное трение и создается запас надежности по толщине
масляного слоя. Следовательно, табличное значение Smin=72 мкм для
выбранной посадки можно принять за SminF=72 мкм.
Теперь
определим наибольший функциональный зазор по формуле (2.8) /4/ при t=500C:

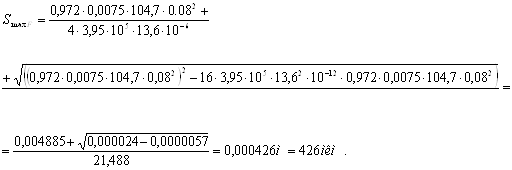
Проверим,
обеспечивается ли при этом зазоре жидкостное трение. Найдем c, hmin, kж.т.:
;
;
;
;
.
Расчеты
показывают, что жидкостное трение обеспечивается.
Запас
на износ определяем по формуле (2.12) /4/ :
, где , ;
.
Строим
схему полей допусков для посадки с зазором с указанием SminТ, SmaxТ, SminF, SmaxF, Sи (рис.2.1.).
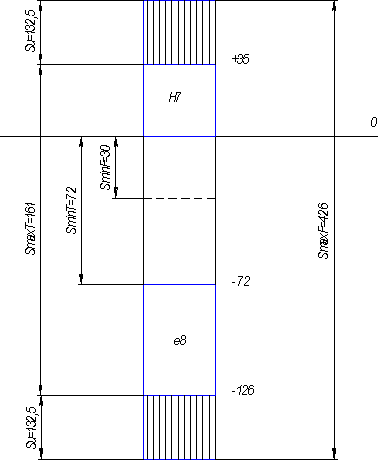
Рис.2.1 Схема
расположения полей допусков деталей при
посадке с зазором.
3.
Расчет посадки с натягом
Задание.
Рассчитать и выбрать посадку с натягом для соединения вала и втулки (d=60мм, d1=0мм, d2=240мм, l=50мм), которое
работает под воздействием крутящего момента Мкр=8Н×м. Запрессовка механическая. Материал обеих деталей - сталь 45.
Определяем
рэ по формуле (3.4) /4/:
,
где - крутящий момент
стремящийся повернуть одну деталь относительно другой (Н м);
- осевое продольное сдвигающее
усилие (Н). В нашем случае равно нулю;
d – номинальный диаметр соединения (м);
l – длина соединения (м);
f – коэффициент трения.
Определяем
коэффициенты Ламе по формулам (3.5) и (3.6) /4/:
;
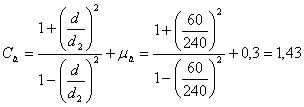
где и - коэффициенты Пуассона
для материалов деталей соединения.
Определяем
Nmin по формуле (3.1) /4/:

где и - модуль упругости
материалов соединяемых деталей, Па.
Находим
поправки к расчетному натягу, используя формулы (3.7) и (3.8), и определяем NminF по формуле (3.9)
/4/:

Принимаем
ut=0 и uц=0, исходя из условий задачи.
 
Определяем
допустимое удельное давление на контактирующих поверхностях по формулам (3.10)
и (3.11) /4/:


В
качестве рдоп выбирается .
Определяем
величину наибольшего натяга Nmax по формуле
(3.12):

Находим
поправки к наибольшему натягу и определяем NmaxF по формуле (3.13)
/4/:
u=15мкм, ut=0, uц=0, uуд=0,78

Выбираем
по таблице 1.49 /1/ посадку по наибольшему функциональному натягу NmaxF, при которой
создавался бы запас прочности соединения и запас прочности деталей: Æ60 H7/s6, для которой NmaxT=72 мкм (£NmaxF), NminT=23 мкм (³NminF)
Определяем
для выбранной посадки запас прочности соединения при сборке и при эксплуатации
по формулам (3.14) и (3.15) /4/:


Для
правильно выбранной посадки запас прочности соединения при сборке Nз.с. всегда должен
быть меньше запаса прочности соединения при эксплуатации Nз.э., потому что Nз.с. нужен только в
момент сборки для случая возможного снижения прочности материала деталей и
увеличения силы запрессовки из-за перекоса деталей, колебания коэффициента
трения и т.д.
Строим
схему расположения полей допусков выбранной посадки (рис.3.1)
Изменить
рисунок согласно расчетам
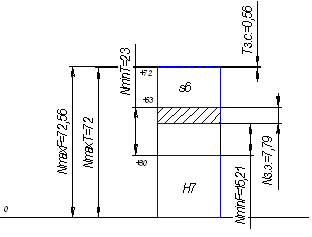
Рис.3.1. Схема
расположения полей допусков деталей при посадке с натягом
4.
Расчет размерных цепей
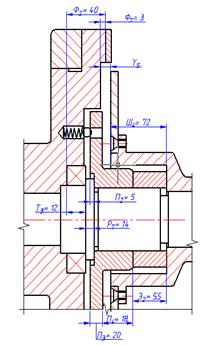
Для расчета размерной
цепи используем метод максимума-минимума.
Назначим допуски, и
предельные отклонения на размеры если допуски на зазор Y5 составляют: верхнее +0,2; нижнее -0,3.
Определяем величину
зазора Y5

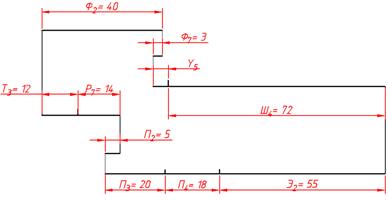
Y5 – является замыкающим звеном. Зазор
должен быть в пределах 5,2 мм до 4,7 мм. Поле допуска на размер 500 мкм
Таблица 4.1.
Аi ном, мм
|
I, мкм |
IT9, мкм |
Аi мм принятое
|
Т3=12 →
|
1,08 |
43 |

|
Р7=14 →
|
1,08 |
43 |

|
П3=20 →
|
1,31 |
52 |

|
П4=18 →
|
1,31 |
43 |

|
Э2=55 →
|
1,86 |
74 |

|
Ф7=3 →
|
0,55 |
25 |

|
П2=5 ←
|
0,73 |
30 |

|
Ш4=72 ←
|
1,86 |
74(128) |

|
Ф2=40 ←
|
1,56 |
62 |

|
Σ |
11,34 |
446(500) |
|
Определяем среднее
количество единиц допуска:
единиц.
Определяем квалитет,
данное количество единиц соответствует:
IT9=45 единиц
Допуски составляющих
размеров находим в табл. 1.8 /1/ и записываем их в таблицу.
Сумма допусков
составляющих звеньев получилась меньше допуска замыкающего звена. Чтобы
уравнение удовлетворялось увеличим допуск одного из составляющих звеньев. Этим
звеном будет – Ш4.

Занесем принятые значения
допусков в таблицу.
Назначим отклонения
звеньев Т3 , Р7 , П3 , Э2 в минус
т.к. они являются охватываемыми, а для звеньев П2, Ф2, П4,
Ф7 , в плюс охватываемые. Допуск на замыкающее звено "плюс-минус"
следовательно допуск на звено Ш4 рассчитаем.






Заносим полученные данные
в таблицу.
Размер замыкающего звена
находится в пределах допуска указанного в условии задания. При необходимости
можно увеличить допуски на все звенья, рассчитав цепь с помощью "теоретико-вероятностного"
метода.
Произведем расчет
размерной цепи теоретико-вероятностный методом, данный метод позволяет
назначать менее жесткие допуски составляющих звеньев при том же допуске
конечного звена.
Определяем величину
зазора Y5

Y5 – является замыкающим звеном. Зазор
должен быть в пределах 5,2 мм до 4,7 мм. Поле допуска на размер 500 мкм.
Таблица 4.2.
Аi ном
мм
|
i
мкм
|
i2
|
IT11
мкм
|
(IT)2
|
TAi мкм
принято
|
Аi мм
принятое
|
Т3=12 →
|
1,08 |
1,17 |
110 |
12100 |
110 |

|
Р7=14 →
|
1,08 |
1,17 |
110 |
12100 |
110 |

|
П3=20 →
|
1,31 |
1,72 |
130 |
16900 |
130 |

|
П4=18 →
|
1,31 |
1,72 |
110 |
12100 |
110 |

|
Э2=55 →
|
1,86 |
3,46 |
190 |
36100 |
190 |

|
Ф7=3 →
|
0,55 |
0,3 |
60 |
3600 |
60 |

|
П2=5 ←
|
0,73 |
0,53 |
75 |
5625 |
75 |

|
Ш4=72 ←
|
1,86 |
3,46 |
190 |
36100 |
355 |

|
Ф2=40 ←
|
1,56 |
2,43 |
160 |
25600 |
160 |

|
Σ |
|
15,9 |
|
160225
(250000)
|
|
|
Определяем среднее
количество единиц допуска:

Определяем квалитет,
данное количество единиц соответствует:
IT11=100 единицы
Допуски составляющих размеров
находим в табл. 1.8 /1/ и записываем их в таблицу.
Так как меньше допуска на размер
замыкающего звена, то увеличим допуск на один из размеров - Ш4.

Занесем принятые значения
допусков в таблицу.
Назначим отклонения
звеньев Т3 , Р7 , П3 , Э2 в минус
т.к. они являются охватываемыми, а для звеньев П2, Ф2, П4,
Ф7 , в плюс охватываемые. Допуск на замыкающее звено "плюс-минус"
следовательно допуск на звено Ш4 рассчитаем. Рассчитаем середины полей допусков.











Рассчитываем верхнее и
нижнее отклонение звена Ш4:


Заносим полученные данные
в таблицу.
Литература
1. Допуски и посадки: Справочник в 2-х ч./ Под ред. В.Д.Мягкова. – 5-е
изд., перераб. и доп. - Л.: Машиностроение, 1978. – 544с.
2. Е.В.Перевозникова, М.П.Худяков. Метрология, стандартизация,
сертификация. Учебное пособие. Часть 1 "Метрология". Северодвинск.
Севмашвтуз, 2007. – 88 с.
3. Е.В.Перевозникова, М.П.Худяков. Метрология, стандартизация,
сертификация. Учебное пособие. Часть 3 "Сертификация". Северодвинск.
Севмашвтуз, 2007. – 100 с.
4. Перевозникова Е.В. Методические указания по выполнению
курсовой работы по дисциплине "Метрология, сертификация и стандартизация"
на тему "Точностные расчеты". Северодвинск: Севмашвтуз, 2004 – 46 с.
|